FACILITY
We take pride in our reputation for excellent customer service, quality products, and innovative solutions.
LATEST NEWS
Corporate Presentation
Sustainability Report
Design
Design Capabilities & Facilities
Design and manufacture of transformers is carried out by a team of well experienced electrical and mechanical engineers, using state of the art design tools and techniques.
Using high level CAD software we develop drawings in 2D and 3D to get effective results for customer submission as well as for the manufacturing purpose.
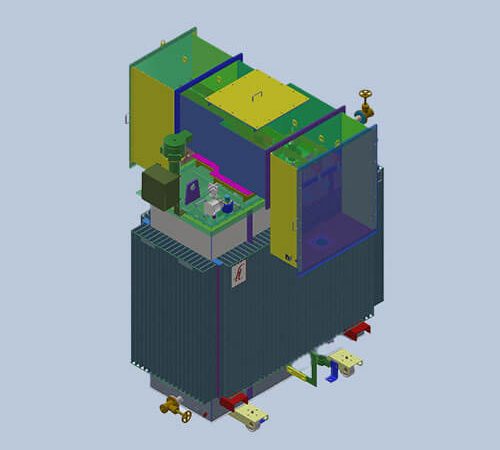
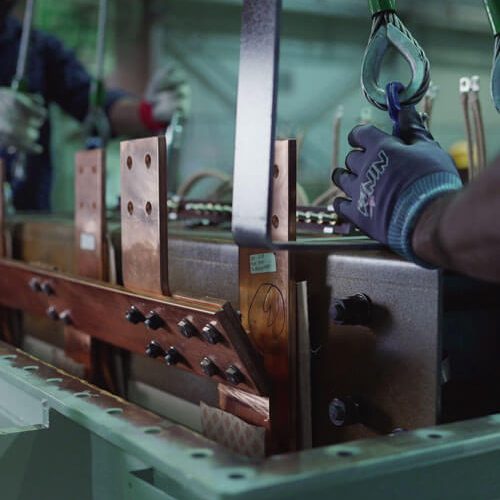
Manufacturing
The core employs a mitred step-lap design ensuring minimum noise and loss level
The Core
Each transformer core is produced by using interleaved laminations of cold rolled, grain orientated, low loss electrical sheet steel conforming to BSEN 10107 and other international standards. The core employs a mitred step-lap design ensuring minimum noise and loss levels with uniform flux distribution throughout the magnetic circuit.
Windings & Insulation
All windings are manufactured to exact standards in order to maintain strict dimensional tolerances. Clamping to a pre-determined load pressure during manufacture ensures that each winding is able to withstand the excessive axial forces which may result from external and short-circuit events.
All principal components of insulation are prefabricated from electrical grade insulating board and are pre-shrunk to ensure electrical and mechanical stability throughout the temperatures found in operational service.
The completed core-coil assembly is dried in a PLC controlled vacuum drying chamber
Core-Coil Assembly
Tanking
Final Assembly
When the tanking process is completed all accessories are fitted.
Windings & Insulation
- Bushings (Oil to Oil, Oil to SF6, Oil to Air Condenser, Porcelain, Plug-in type, Monoblock)
- Conservator with hydrocompensator (Air bag)
- Maintenance free breathers
- Remote Control Panels for automatic voltage regulation of OLTC
- Hydran/Callisto online gas monitoring devices
- Other customer specific fittings/instruments
After the final assembly process is completed the oil is filtered again and allowed to settle before the transformer is moved to the test bay.
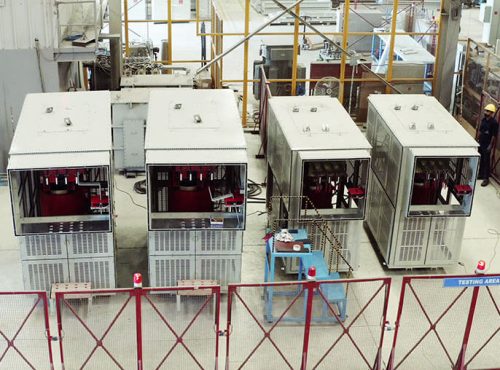
Testing & Inspection
Test Facilities Available
Routine Tests
- Bushings (Oil to Oil, Oil to SF6, Oil to Air Condenser, Porcelain, Plug-in type, Monoblock)
- Conservator with hydrocompensator (Air bag)
- Maintenance free breathers
- Remote Control Panels for automatic voltage regulation of OLTC
- Hydran/Callisto online gas monitoring devices
- Other customer specific fittings/instruments
Routine Tests
- Measurement of insulation resistance
- Measurement of voltage ratio and check of phase displacement
- Measurement of winding resistance
- Measurement of short-circuit impedance and load loss
- Measurement of no-load loss and current
- Induced voltage withstand test (IVW)
- Applied voltage test (AV)
- Breakdown voltage test on transformer oil as per IEC- 60296
- Oil tightness (Oil leakage) test
Type / Special Tests as per IEC-60076
- Temperature rise test
- Full wave / Chopped wave lightning impulse test
- Noise level measurement test
- Measurement of dissipation factor of the insulation system capacitances. (tan δ)
- Partial discharge test
- Measurement of harmonics of the n-load current
- Measurement of zero sequence impedance
- Pressure Test on Tank
- Tests on Painting work
- Sweep Frequency Response Analysis Test (SFRA)
Quality Assurance
Federal Transformers Co. LLC has approved Quality and EHS Management Systems conforming to ISO 9001, ISO 14001, ISO 45001 and OSHAD-SF (Abu Dhabi Occupational Safety and Health System)
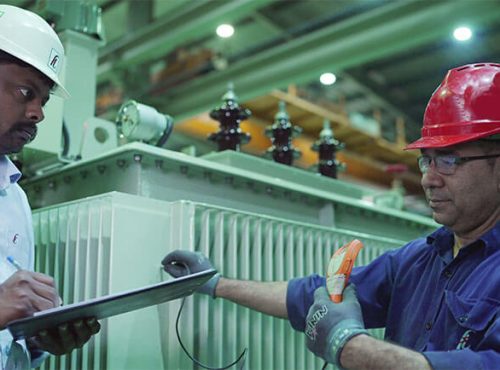